
Crushing And Separation Of The Ore Of Iron


Crushing And Separation Of The Ore Of Iron

Mineral processing
Mineral processing can involve four general types of unit operation: comminution particle size reduction; sizing separation of particle sizes by screening or classification; concentration by taking advantage of physical and surface chemical properties; and dewatering solid/liquid separation. In all of these processes, the most important considerations are the economics of the proceThis chapter introduces the principle of how low-grade iron ores are upgraded to high-quality iron ore concentrates by magnetic separation. Magnetite is the 9 Developments in the physical separation of iron ore
احصل على السعر
Transforming iron ore processing ScienceDirect
In the recent past, iron ore resources from Brazil consisted of relatively high-grade iron ore, commonly processed via multi-stage crushing/screening, Iron ore flotation. Froth flotation is an efficient method to remove impurities from iron ore when the valuable and impurity minerals are liberated. The separation is Physiochemical separation of iron ore ScienceDirect
احصل على السعر
Iron ore
Iron ores [1] are rocks and minerals from which metallic iron can be economically extracted. The ores are usually rich in iron oxides and vary in color from dark grey, bright yellow, or deep purple to rusty red. The iron 1 Introduction. The effectiveness of simultaneous effect of mechanical load and electric field of ultra-high frequency (UHF) in the process of iron ore crushing is substantiated in Research into the crushing and grinding processes of iron ore with
احصل على السعر
Dry Magnetic Separation of Iron Ore of the Bakchar Deposit
Currently, the development of iron ore of the Bakchar deposit (Tomsk region) is considered promising because of the extremely large reserves of iron ore. Iron ore beneficiation mainly includes crushing, grinding, gravity separation, flotation and magnetic separation. Magnetic separation is one of the main methods for iron ore separation. Combining the Iron Ore Beneficiation Plant JXSC Machinery
احصل على السعر
11.23 Taconite Ore Processing
As the iron ore minerals are liberated by the crushing steps, the iron-bearing particles must be concentrated. Because only about 33 percent of the crude taconite becomes a shippable product for iron making, a large amount of gangue is generated. Magnetic separation and flotation are the most commonly used methods for concentrating It is easy to extract iron from this kind of haematite by using gravity separation and magnetic separation. Medium-grained hematite refers to iron ore with an embedded particle size between 0.02 How to Extract Iron from Hematite: Methods and Plants
احصل على السعر
Transforming iron ore processing ScienceDirect
In the recent past, iron ore resources from Brazil consisted of relatively high-grade iron ore, commonly processed via multi-stage crushing/screening, gravimetric concentration, magnetic separation, and reverse flotation. However, the high-grade iron ore reserves are in decline, resulting in the need to process the lower grade itabirite iron The iron ore thickening process involves the steps of crushing and screening, grinding and classification, hydrocyclone separation and desliming, flocculation, sedimentation, filtrationWhat is the iron ore thickening process? LinkedIn
احصل على السعر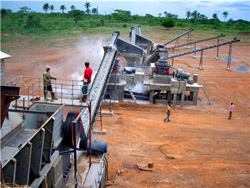
Crushing, Grinding and Concentration of the Ore Class Notes
If either ore or the gangue (one of these two) is attracted by a magnet then ore can be separated from the impurities with the help of magnetic separation method. For example: 1) The magnetic impurities such as iron and manganese tungstates (FeWO 4 ,MnWO 4 ) present in tin stone (SnO 2,non-magnetic) are separated by this method.crushed magnetite ores. Therefore, here, we consider the use of less costly drum magnetic separators, modernized to work with waste from the dry processing of such ores. Cas-caded drum magnetic separators are proposed, which allow to achieve comparable results with [16,17] on the beneficiation of iron-containing ore magnetic Beneficiation of Magnetically Separated Iron-Containing Ore Waste
احصل على السعر
Transforming iron ore processing Simplifying the comminution
In the recent past, iron ore resources from Brazil consisted of relatively high-grade iron ore, commonly processed via multi-stage crushing/screening, gravimetric concentration, magnetic separation, and reverse flotation. However, the high-grade iron ore reserves are in decline, resulting in the need to process the lower grade itabirite iron Published Apr 9, 2019. + Follow. Generally, iron ore with a grade of less than 50% needs to go through a dressing process before it can be sent to smelting for utilization. After the mined oreGuide for iron ore dressing LinkedIn
احصل على السعر
Dry Magnetic Separation of Iron Ore of the Bakchar Deposit
Currently, the development of iron ore of the Bakchar deposit (Tomsk region) is considered promising because of the extremely large reserves of iron ore. Ores of this deposit are related to the high-grade type and expected to have a magnetic concentration for iron extraction. The main task of magnetic separation is to increase kefid product the iron ore crushing plant for customers. kefid is an important iron ore crusher and iron ore crushing plantmanufacturer, we can design the complete Metallurgy process, crushing of ore, concentration of ore, gravity separation and levigation with examples.crushing of ore Mining & Quarry Plant
احصل على السعر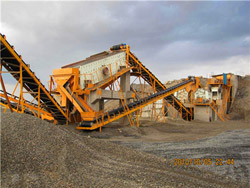
Basics of mineral processing PPT SlideShare
8 Size reduction of ores is normally done in order to liberate the value minerals from the host rock. it is done through Crushing and grinding of ore and minerals. this is also called as liberation the 3.Mining: Iron ore is extracted from the ground using a variety of mining techniques, including open-pit mining, underground mining, or a combination of both, depending on the depth and locationHow is iron mined and refined? LinkedIn
احصل على السعر
Study on Quantitative Separation Method of Grinding MDPI
Based on batch grinding method and normalization idea, a conical ball mill is used and a quantitative separation method of grinding characteristics of multi-component complex ore is proposed. The results show that the feed sizes of polymetallic complex ore have an obvious influence on the particle size distribution of intermediate grinding Iron Ore Dressing. The iron ore dressing process is aimed at the processing of iron ore materials, which is divided into crushing and screening, grinding and classification, separation, and dehydration.Crushing and screening refers to the crushing and screening of iron ore to ensure that the particle size of crushed ore can provide ore that meets the Iron Ore Processing JXSC Mineral
احصل على السعر
Beneficiation of Iron Ores IspatGuru
Fig 3 Types of processing ores. The wet processing (Fig 4) is normally practiced for low / medium grade (60 % Fe to 63 % Fe) hematite iron ore. The wet process consists of multi-stage crushing followed by different stages of washing in the form of scrubbing and / or screening, and classification etc., but the advantage is only partial To know more about this process and iron ore mining, contact us and learn all about iron ore, polyurethane and the associated processes of processing iron ore. Stockpiling And Crushing. Before being crushed, the iron ore must first be broken up to an F 80 grind size. The crushed ore is then sent to a stockpile after being crushed.Iron Ore Processing Top 6 Steps of Iron Ore Processing
احصل على السعر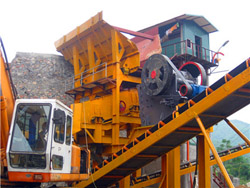
Beneficiation of an iron ore fines by magnetization roasting and
These iron ores contain many detrimental impurities and are difficult to upgrade to make suitable concentrates for the blast furnace. In this paper, the beneficiation of a low-grade hematite ore fines containing carbonates with magnetization roasting and magnetic separation was proposed and studied. The hematite and siderite are almostA Possible Comminution Circuit for the Iron Ore Plant Since the receiving Ajaokuta blast furnace requires coarse concentrate for efficient operation, the fine ore material stored in bins may be(PDF) Design of Comminution Circuit for Optimum ResearchGate
احصل على السعر
Crushing and separation of the ore of iron
Once the iron minerals are separated, they are further processed through various steps to produce iron ore concentrate, which is then used in the production of iron and steel. Overall, the crushing and separation of iron ore are vital steps in the extraction and processing of iron. These processes ensure that the desired iron minerals are
احصل على السعر