
filling ratio of grinding mill


filling ratio of grinding mill
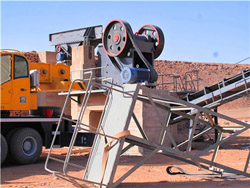
An improved method for grinding mill filling
If just the five measurements along the mill axis were used to represent the surface-to-roof height as would be the case when measurements are carried out with a mill entry the averages would be 8.93 m (20.0% filling) and 9.54 m (14.5% filling) for The filling ratio, particle to ball ratio, time domain features and sample entropy are features extracted from the signal, providing input to a support vector An improved method for grinding mill filling
احصل على السعر
An improved method for grinding mill filling measurement and
The filling ratio, particle to ball ratio, time domain features and sample entropy are features extracted from the signal, providing input to a support vector The grinding media filling ratio was kept constant at 0.8 in all of the mills except for the accelerator mill, which was operated at a filling ratio of 0.7 due to Mill, material, and process parameters ScienceDirect
احصل على السعر
CN103721799A Determination method for filling ratio of
The method is characterized by including the following steps: a filling ratio-reducing experiment stage is adopted to reduce load carrying of balls, inflection point The L/D ratio of the ball mill was varied in four steps of 1.75, 2.1, 2.79 and 3.49, and the ball charge filling ratio was varied in three steps of 15%, 20% and Optimization of continuous ball mills used for finish-grinding of
احصل على السعر
Optimization of continuous ball mills used for finish
The results of extensive investigations carried out on industrial semi-finish-grinding plants indicated that the specific power consumption of the ball mill could The filling ratio, particle to ball ratio, time domain features and sample entropy are features extracted from the signal, providing input to a support vector Assessing load in ball mill using instrumented grinding media
احصل على السعر
Efficiency and grinding media filling level Request PDF
Since delivery time for parts to repair the damaged drive was lengthy, a decision was made to reduce the charge in the ball mill from approximate 32% filling The ratio effect of total volume of balls and powders with respect to volume of vial has not been deeply considered by the researchers for ball milling process. The Filling ratio of vial SpringerLink
احصل على السعر
Metals Free Full-Text A Comparative Study of Energy MDPI
An evaluation of Relo grinding media (RGM, Reuleaux tetrahedron-shaped bodies) performance versus standard grinding media (balls) was made through a series of grinding tests, including a slight modification of the standard Bond test procedure. Standard Bond tests showed a reduction in the Bond ball mill work index (wi) of the mineral The relative motion and collision between grinding media in a wet-stirred accelerator mill are modelled using the discrete element method (DEM) coupled with computational fluid dynamics (CFD). The local average normalized grinding media velocity profile is employed to divide the grinding chamber into four volumes, which facilitates Minerals Free Full-Text Simulation of Grinding Media Motion
احصل على السعر
DEPENDENCE OF THE BOND WORK INDEX ON THE FILLING RATIO
grinding cycles are used to calculate the work index (Wi) by Karra's algorithm [4] and modified Kapur's algorithm [5]. It should be known that this method does not need any special feed preparation, therefore, the effect of ore filling ratio on the work index was studied at filling ratios of 36.4%, 60% and 90%In wet milling, the presence of a pool of slurry is generally the result of mill overfill. The effects of overfilling on milling kinetics have been examined. Assessment of milling efficiency has also been made. To this end, batch grinding tests were carried out at 75% of critical speed. A laboratory mill, filled with 20 mm balls, was used forEffects of slurry pool volume on milling efficiency ScienceDirect
احصل على السعر
Impact of Operating Parameters on the Breakage Process of Talc
This manuscript aimed to examine the impact of operating parameters on the wet grinding of talc in a vertical-type stirred media mill. Within the scope of the research, the effects of operating parameters including media filling ratio, solid mass fraction, grinding media size, and grinding time were studied. The findings were 2018 Target Operating Hours in Cement industry S.No. Department Operating hrs/Day 1. Mines* 10 2. Crusher* 10 3. Raw Mill (Ball mill, VRM) 21 Raw mill (Roller press) 20 4. Coal mill (Ball mill, VRM) 21 5.Ball Mill Performance & Efficiency Formulas INFINITY FOR CEMENT EQUIPMENT
احصل على السعر
Impact of ball filling rate and stirrer tip speed on milling iron ore
Based on the specific productivity and grinding efficiency, the appropriate grinding parameters were ascertained as follows: material ball ratio of 0.7, ceramic ball medium size ratio (10 mm: 15 mm: 20 mm = 3:2:5), stirring speed of 110 rpm, grinding concentration of 50%, and medium filling rate of 90%.The L/D ratio of the ball mill was varied in four steps of 1.75, 2.1, 2.79 and 3.49, and the ball charge filling ratio was varied in three steps of 15%, 20% and 25%. The experiments clearly indicated that the optimal L/D ratio and the optimal ball charge filling ratio are different for each feed fineness.Optimization of continuous ball mills used for finish-grinding of
احصل على السعر
Effect of grinding media properties and stirrer tip speed on the
Based on the specific productivity and grinding efficiency, the appropriate grinding parameters were ascertained as follows: material ball ratio of 0.7, ceramic ball medium size ratio (10 mm: 15 mm: 20 mm = 3:2:5), stirring speed of 110 rpm, grinding concentration of 50%, and medium filling rate of 90%.Maximum ball size (MBS) Please Enter / Step-to Input Values. Mill Feed Material Size F, mm. Specific weight of Feed SG, g/cm 3.ball mill calculations, grinding media filling degree, ball size, mill
احصل على السعر
Assessing load in ball mill using instrumented grinding media
The filling ratio, ratio of particle to ball and mineral weight were varied to control the mill load. The initial ratio of grading ball was 30 mm: 40 mm: 50 mm: 70 mm = 30: 20: 30: 20. It should be noted that the diameter of instrumented grinding media is 70 mm. Rotation speed of cement ball mill was set to 80%.At low material filling ratios there is a reduced number of ball-to-material contacts, due simply to an absence of material in the nip points, They used kWh/t of mill throughput as a bench mark given that they were grinding to a mill exit of 1800 cm 2/g. All mills were running at 55% to 75% of critical speed.Cement Mill Ball Mill Dynamics PDF Mill (Grinding Scribd
احصل على السعر
Effect of grinding media on the milling efficiency of a ball mill
grinding tests were conducted in a smooth surface cylin-drical steel mill of 215 mm diameter and 190 mm long. The grinding media consisted of three different-sized steel balls having a density of 7.68 g/cm3 and diameters of 19.5, 38, and 50 mm. The Bond work index (Wi) of the quartz sample was determined based on two grinding tests.The objective of this paper is to investigate the effect of ball filling and ratio of feed to grinding balls on the kinetic of grinding of ferronickel slag in a laboratory scale ball mill. The experiments were started by crushing the ferronickel slag samples using a roll crusher to produce -3 mesh (-6.7 mm) product. This product, after sampling and sample dividing Kinetic study of ferronickel slag grinding at variation of ball filling
احصل على السعر
Chapter 6 Wet Grinding in Stirred Media Mills ScienceDirect
Only the curve for the filling ratio of 0.85 lies slightly higher than the one for the filling ratio of 0.8 because at a filling ratio of 0.85 the freedom of motion is already too small. Therefore, at a filling ratio of approximately 0.8 the specific energy to produce a given product fineness is the lowest. Download : Download full-size imageThe grinding test conditions were listed as follows: grinding time was set at 2 min, 4 min, 6 min, 8 min and 10 min; the grinding concentration at 65%; the filling ratio at 32%; the grinding particle size at −1.7 mm and the rotational speed ratio at 80%.Minerals Free Full-Text Grinding Optimization of Cassiterite
احصل على السعر
Research on Grinding Law and Grinding Parameters Optimization
For Gaofeng ore, the optimized grinding conditions are grinding time 3.8 min, grinding concentration 73% and filling ratio 34%. Next Article in Journal Deformation Termination of the Kanggur Ductile Shear Zone in Eastern Tianshan, NW China: Insights from U-Pb Dating of Zircon and ApatiteAs a result of the present research, the following optimum grinding test conditions were determined: 65% media filling ratio, 40% solid mass fraction, 1 mm grinding media size, and 120 minChapter 6 Wet Grinding in Stirred Media Mills Request PDF
احصل على السعر
(PDF) Energy-Model and Life Cycle-Model for Grinding Processes
ratio (70–80%) and grinding time (5–20 min) were adjusted in the applied stirred ball mill. The fineness of grinding limestone products was analyzed by a laser deflection particle sizer .An evaluation of Relo grinding media (RGM, Reuleaux tetrahedron-shaped bodies) performance versus standard grinding media (balls) was made through a series of grinding tests, including a slight modification of the standard Bond test procedure. Standard Bond tests showed a reduction in the Bond ball mill work index (wi) of the mineral Metals Free Full-Text A Comparative Study of Energy MDPI
احصل على السعر