
milling in mineral processing


milling in mineral processing

A process mineralogy approach to study the efficiency of
In order to study the mineralogy of milling process in the molybdenum processing circuit, samples of feed (middle thickener underflow) and product of open Mineral milling with Atritor. Our state-of-the-art mineral milling solutions are designed to meet diverse processing needs. We offer solutions for dry milling, fine milling, Mineral Milling and Processing Atritor
احصل على السعر
(PDF) Overview of Mineral Processing Methods
The first process that most of the ores or minerals undergo after they leave any mine, is mineral processing or mineral/ ore Special Issue "Advances in Ore Processing Technologies: Crushing, Milling and Separation". A special issue of Minerals (ISSN 2075-163X). This special Minerals Special Issue : Advances in Ore Processing MDPI
احصل على السعر
Modeling of Bauxite Ore Wet Milling for the
Size reduction is a necessary operation in mineral processing plants and provides the desired size for separation operations and the liberation of the valu The fields of machine learning (ML) and artificial intelligence (AI) have recently seen a number of highly-publicised successes, with systems capable of Machine learning applications in minerals processing: A
احصل على السعر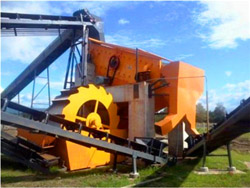
Reduction of Fragment Size from Mining to Mineral Processing: A
The effects of rock fragmentation on the whole size reduction chain from mining to mineral processing are described. The main factors influencing rock In the field of extractive metallurgy, mineral processing is the process of separating commercially valuable minerals from their ores. Depending on the processes used in Mineral processing
احصل على السعر
MINERAL PROCESSING MILLING Internet Archive
Mineral Processing –Milling Intermediate Technology Development Group 2 foodstuffs, because a comprehensive publication already exists in the area of grain milling (see final section on resources). Material Characteristics When a material is to be milled there are certain characteristics which have to be taken into account. These include theThe ball mill is a rotating cylindrical vessel with grinding media inside, which is responsible for breaking the ore particles. Grinding media play an important role in the comminution of mineral ores in these mills. This work reviews the application of balls in mineral processing as a function of the materials used to manufacture them and the A Review of the Grinding Media in Ball Mills for Mineral Processing
احصل على السعر
A process mineralogy approach to study the efficiency of milling
A new look at mineral maps and the potential relationships of extracted data to mineral processing behaviours. in Ninth International Congress for Applied Mineralogy. AusIMM. 429–432 (2008Introduction To Toll Milling. Milling is one of the major toll services for minerals offered by African Pegmatite, alongside drying and granulation. Processing minerals requires specialised machinery that’s suited for the type of mineral being milled. There are quite a few machines for mineral milling and each has a unique specialisation.Toll Milling and Mineral Processing African Pegmatite
احصل على السعر
Energy Use of Fine Grinding in Mineral Processing SpringerLink
Fine grinding, to P80 sizes as low as 7 μm, is becoming increasingly important as mines treat ores with smaller liberation sizes. This grinding is typically done using stirred mills such as the Isamill or Stirred Media Detritor. While fine grinding consumes less energy than primary grinding, it can still account for a substantial part of a mill’s Mineral processing is the art and technology of treating ores from mining areas in order to separate the valuable minerals from waste rock. It includes processes to provide a more concentrated material for the procedures of the following extractive metallurgy. The three main processes to increase the concentration of minerals are leachingReagents for Mineral Processing Borregaard
احصل على السعر
Benefits of process control systems in mineral processing
This article focuses on quantifying the benefits of process control systems in the mineral processing industry. The benefits sought in the mineral processing industry are the same sought in other commodity industry, namely throughput gain, process stability, energy consumption reduction, and increased yield. A survey by Simulations of minerals processing systems, such as milling circuits (le Roux et al., 2013, Wakefield et al., 2018) and leaching processes (Dorfling et al., 2013a, Dorfling et al., 2013b, Strydom et al., 2018) could be used as benchmarks for testing of data-based modelling and fault detection and diagnosis techniques; simulations for testing Machine learning applications in minerals processing: A review
احصل على السعر
Development of ore sorting and its impact on mineral processing
The energy costs required to refine metal values contained in ore to concentrates constitute the majority of the cost to produce metals. On average across the mining industry, 44% of the total electricity consumption is dedicated to crushing and milling activities (Fig. 1).Size reduction operations, nearly 150 × 10 9 kW h, are the largest SYNOPSIS. In 2017, Petra Diamonds completed the construction and commissioning of a modern, fit-for-purpose diamond processing plant at Cullinan Diamond Mine (CDM). The design of CDM's milling circuit is unconventional in that it comprises an autogenous (AG) mill with a grate discharge with large ports, low-revolution jaw crushers, and highThe new Cullinan AG milling circuit a narrative of progress SciELO
احصل على السعر
Introduction to Mineral Processing or Beneficiation
Autogenous (AG) and Semi-Autogenous (SAG) milling has seen increased use in recent years, especially in large mineral processing operations. These mills typically have a large diameter Due to the high consumptions of energy and materials by ball milling, it is necessary to avoid useless grinding. Overbreakage will result in the loss of valuable minerals, low recovery rate, increased wear The Effect of Grinding Media on Mineral Breakage
احصل على السعر
Review on advances in mineral processing technologies suitable
The first comminution stage in a mineral processing plant is crushing, which reduces the size of particles from up to 1 m down to 0.5 cm (depending on the type of milling circuit). Crushing is typically a dry process that makes use of Gyratory, Jaw, and Cone crushers ( Napier-Munn et al., 1996 ), which predominantly make use of impact MINERAL PROCESSING. MILLING Introduction Milling, sometimes also known as fine grinding, pulverising or comminution, is the process of reducing materials to a powder of fine or very fine size. It is distinct from crushing or granulation, which involves size reduction to a rock, pebble or grain size. Milling is used to produce a variety of materials which either Milling in The Mineral Process PDF Mill (Grinding) Materials
احصل على السعر
Closed Circuit Grinding VS Open Circuit Grinding 911
This type of grinding is the most common circuit found in mineral processing facilities, mainly because a lot of ores and product requirements are not suitable for open circuit grinding. Some advantages presented by grinding in closed circuit are that this arrangement usually results in higher mill capacity and lower power consumption per In terms of this concept, the energy efficiency of the tumbling mill is as low as 1%, or less. For example, Lowrison (1974) reported that for a ball mill, the theoretical energy for size reduction (the free energy of the new surface produced during grinding) is 0.6% of the total energy supplied to the mill setup.The energy efficiency of ball milling in comminution
احصل على السعر
Life Cycle Assessment in mineral processing a review of the
The system boundary details the mineral processing stage into the following unit processes: crushing and milling, flotation, leaching and dissolution and precipitation. Data have been derived from a prefeasibility flowsheet from Mkango Resource Ltd, literature, simulation with HSC Chemistry software and ecoinvent and GaBi databases.Comminution represents up to 50% of the total energy consumption in the mineral production process [2]. Moreover, comminution using ball milling is highly inefficient due to heat and mechanicalThe energy efficiency of ball milling in comminution
احصل على السعر
Plant Automation for Energy-Efficient Mineral Processing
The mineral processing sector holds a significant and growing share of the energy balance of the mining industry. Tromans [] reported striking data from the U.S. Department of Energy showing that 39% of the energy footprint of mining operations originated from beneficiation and processing operations in 2004.More recently, the Crushing in Mineral Processing. crushing. Depending of the type of rock ( geometallurgy) to be crushed, there are 2 largely different techniques at your disposition for crushing rocks. In principle, compression crushing is used on hard and abrasive rocks by placing them between a high wear-resistant plate/surface.Crushing in Mineral Processing 911 Metallurgist
احصل على السعر