
grinding polishing robot


grinding polishing robot

A hybrid control strategy for grinding and polishing robot
A hybrid control strategy for grinding and polishing robot is proposed based on adaptive impedance control. Firstly, an electrically Due to the constant force output characteristic of CFM, the grinding head can maintain constant force contact with the workpiece in a specific range of motion to Surface polishing by industrial robots: a review SpringerLink
احصل على السعر
Automatic Grinding and Polishing Using Spherical Robot
Previous research on the polishing process systems are based on traditional grinding machines, which use a dual-drive system (Li et al., 2002). During the This paper firstly introduces the relevant concepts of force control of grinding and polishing robots, including two modes of robot force control, and then elaborates the A Review of Robot Grinding and Polishing Force Control Mode
احصل على السعر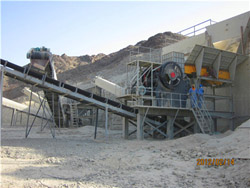
(PDF) Compliant grinding and polishing: A review ResearchGate
However, applying position-based industrial robots directly to grinding and polishing processes involving contact motion is not straightforward [2, 12].Successful robotic grinding, de-burring and finishing applications means applying the proper amount of force onto the part. Insufficient force wastes time and valuable abrasive media while too Robotic Grinding, De-Burring and Finishing
احصل على السعر
Review on robot-assisted polishing: Status and future trends
To achieve nanometric surface roughness, high-precision polishing is mandatory. Compared with the conventional polishing techniques, the robot-assisted Aiming at the grinding and polishing robot system scheme, a compliant motion control strategy is proposed. The control strategy is divided into two parts. The first part considers the process of robot moving to the workpiece in free space, the purpose is to reduce the impact force generated when the grinding and polishing robot hits the A hybrid control strategy for grinding and polishing robot
احصل على السعر
Removal, Polishing, Finishing, Deburring, Cutting Robots
Yaskawa Motoman’s extensive product line of high-performance material removal robots includes a variety of application-specific and general-purpose models that are ideal for material removal, surface preparation and finishing operations, including grinding, finishing, polishing, sawing, degating, waterjet removal, etc. Payloads from 6-35 kg.Through automated grinding you can achieve more consistent part quality, increased throughput and long-term cost savings over manual grinding. Partner with 3M and our robotics experts will help guide you through the automation journey. We have the long-lasting, fast-cutting abrasives and industry knowledge you’ll need for a successfulRobotic Grinding 3M Abrasives
احصل على السعر
A Review of Robot Grinding and Polishing Force Control Mode
2022 IEEE International Conference on Mechatronics and Automation (ICMA) The working conditions in grinding and polishing operations are complex and harsh, and it is gradually becoming a trend to replace manual grinding and polishing with robots. This paper firstly introduces the relevant concepts of force control of grinding Abstract. Abstract: Low-cost and high-dexterity robots were used in field of grinding and polishing more and more widely. Compliance control of grinding and polishing forces for robots were the key to reduce surface roughness of workpieces and obtain high shape accuracy and surface integrity. Main research results of at home and abroad scholarsResearch Progresses of Robot Grinding and Polishing Force
احصل على السعر
A Review of Robot Grinding and Polishing Force Control Mode
A Review of Robot Grinding and Polishing Force Control Mode. Pages 1413–1418. Previous Chapter Next Chapter. ABSTRACT. The working conditions in grinding and polishing operations are complex and harsh, and it is gradually becoming a trend to replace manual grinding and polishing with robots.Aiming at the grinding and polishing robot system scheme, a compliant motion control strategy is proposed. The control strategy is divided into two parts. The first part considers the process of robot moving to the workpiece in free space, the purpose is to reduce the impact force generated when the grinding and polishing robot hits the A hybrid control strategy for grinding and polishing robot
احصل على السعر
Robotic Grinding & Automated Material Removal Applications
Robotic Offroad Bumper Grinding. As an illustration, this video shows how effortless robotic grinding can be. In fact, a robot paired with a PushCorp force compliance device and servo spindle is just what you need to automate your material removal process. This video showcases an AFD310-2 and an STC0605-BT30.At present, the complex components are mainly ground by virtue of manual operation and multi-axis CNC machine tools. Two typical examples of grinding turbine blade and wind blade are shown in Fig. 1.Because of the time- and labor- consuming as well as the harsh operating environment experienced by manual grinding, the multi-axis Robotic grinding of complex components: A step towards
احصل على السعر
A Robotic grinding station based on an industrial manipulator
The robot grinding station has the advantages of high grasping precision and good consistency in the quality of grinding the workpiece. Wang Y., Shen H., et al. Design and experiment of compliant parallel humanoid wrist joint polishing robot. Transactions of the Chinese Society for Agricultural Machinery, 2016. View ArticleDuring the research a spherical robot is used, this is a 6DOF machine (spherical robot) that in this case is going to make grinding and polishing tasks. The use of this machine combined with a CAM software allows maintain the finishing tool always normal to the surface to be finished. 2.1. Finishing Tool.Automatic Grinding and Polishing Using Spherical Robot
احصل على السعر
Robot welding seam online grinding system based on laser
Zhao et al. [20, 21] designed an adsorption mobile robot grinding and polishing system based on binocular cameras to realize the automatic grinding of large structural parts after welding. Chen et al. [ 22 ] extracted the sub-image of the weld prime edge based on Zernike matrix method.DOI: 10.1016/j.rcim.2022.102482 Corpus ID: 253232840; Review on robot-assisted polishing: Status and future trends @article{Ke2023ReviewOR, title={Review on robot-assisted polishing: Status and future trends}, author={Xiaolong Ke and Yongheng Yu and Kangsen Li and Tianyi Wang and Bo Zhong and Zhenzhong Wang and Lingbao Review on robot-assisted polishing: Status and future trends
احصل على السعر
Contact force detection and control for robotic polishing based
Firstly, the polishing experiments based on the pure position control of the robot are carried out on the curved aluminum plate as shown in Fig. 1 to measure the act polishing force. The average velocity of the robot movement along the tangential direction of the curved surface is about 15 mm/s, and the desired polishing force is − 20 N.Perfect Robot Sanding for a variaty of materials with sensitive end effectors / end-of-arm tools Major automotive + aerospace brands rely on our experience. Grinding, sanding, polishing and deburring a wide variety of materials are key operations in numerous industries and branches.Grinding, sanding, polishing, deburring FerRobotics
احصل على السعر
Automated Polishing and Grinding : Advanced Robotic Manufacturing
icontrol.ri.cmu.eduAbstract: Polishing and grinding of metallic parts is an important manufacturing operation in many industrial applications. It rema...Polishing plays an indispensable role in optical processing, especially for large-aperture optical reflective mirrors with freeform surfaces. Robotic polishing requires effective control of the contact force between the robot and the mirror during processing. In order to maintain a constant contact force during polishing, traditional polishing robots Design of Passive Constant-Force End-Effector for Robotic Polishing
احصل على السعر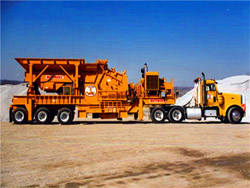
(PDF) Compliant grinding and polishing: A review ResearchGate
However, applying position-based industrial robots directly to grinding and polishing processes involving contact motion is not straightforward [2, 12].Starting from the grinding and polishing process route, this paper introduces the long-term research progress of the Precision Engineering Laboratory of Xiamen University in the field of large-diameter optical aspherical component processing, and introduces in detail the technical and system achievements such as ultra-precision 光学元件超精密磨抛加工技术研究与装备开发 OE Journal
احصل على السعر
Automatic Aluminum Alloy Surface Grinding Trajectory Planning
In this paper, we propose a novel method for planning grinding trajectories on curved surfaces to improve the grinding efficiency of large aluminum alloy surfaces with welds and defect areas. Our method consists of three parts. Firstly, we introduce a deficiency positioning method based on a two-dimensional image and three
احصل على السعر