
the technique of crushing the technique of grinding of fe ed
مسكن > the technique of crushing the technique of grinding of fe ed


the technique of crushing the technique of grinding of fe ed

(PDF) Research into the crushing and grinding processes of iron
Abstract and Figures. Main properties of the processes of iron ore destruction in terms of its simultaneous effect by mechanical load and electric field of process of mechanical crushing and grinding of iron ore. Functions of absorption and dispersion amplitudes are obtained from the vector equation of a harmonic oscillator. Research into the crushing and grinding processes of iron ore with
احصل على السعر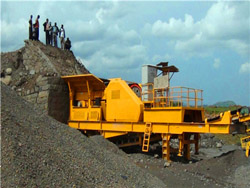
(PDF) SIZE REDUCTION BY CRUSHING METHODS ResearchGate
The objective of this report is to provide the details of size reduction methods involved in mineral processing using crushing equipments.A. Balasubramanian University of Mysore Abstract and Figures The first process that most of the ores or minerals undergo after they leave any mine, is mineral (PDF) Overview of Mineral Processing Methods ResearchGate
احصل على السعر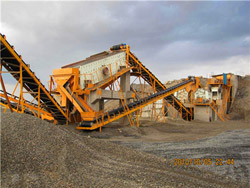
Mechanical Preparation Techniques SpringerLink
1.1 Principle Crushing is used to very quickly produce a fine powder from a bulk material or fine particle using mechanical crushing. This technique is essentially This paper illustrates a technique which can be used to predict the effect of a change in feed grind size on flotation performance. The methodology applied is Grinding and Flotation Circuits Integration and
احصل على السعر
Chapter 2 Mechanical Crushing and Grinding Semantic Scholar
Mechanical alloying/milling technique is characterized by the repeated welding and fracturing of powder particles in a high-energy ball mill, which often results in excessive Mechanochemistry: The Science of Crush. Crushing is an ancient technique for transforming materials that remains central to our lives today. Humans have developed Mechanochemistry: The Science of Crush — Google Arts & Culture
احصل على السعر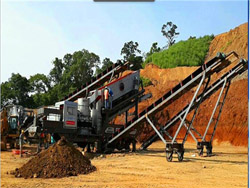
Applications of crushing and grinding-based treatments for typical
The crushing and grinding serve either mainstream or auxiliary role in the processing of the solid wastes. This review summarizes and highlights the developments 1. Introduction. Crushing and grinding are necessary for the processing of minerals that coexist closely with gangue minerals (Gong et al., 2020, Wills and Finch, 2016).Crushing-grinding provides the materials with a suitable particle size and the sufficient liberation of useful minerals for the subsequent separation process (Li and Gao, Effects of grinding media on the flotation performance of cassiterite
احصل على السعر
The influence of grinding technique on the liberation of clinker
In the second sampling period samples were prepared similarly but this time as distribution samples such as − 75 μm, − 63 μm, − 53 μm, − 45 μm, − 38 μm and − 20 μm material.Products of both grinding modes were sieved in the same size classes and attention was paid to get comparable size distributions to eliminate the impact of size Fig 3 Types of processing ores. The wet processing (Fig 4) is normally practiced for low / medium grade (60 % Fe to 63 % Fe) hematite iron ore. The wet process consists of multi-stage crushing followed by Beneficiation of Iron Ores IspatGuru
احصل على السعر
Applications of crushing and grinding-based treatments for
Apparatus and mechanism of crushing/grinding treatment. The crushing and grinding-based treatments are highly dependent on the input of mechanical energy, which could induce the chemical and physicochemical transformations of substances in all states of aggregations (Heinicke, 1986).The models, simulation, and validation were presented during the last decade over various moving particle investigations with thermal convection and disclosed the challenges as well. The present work provides the simulation and validation of the grinding mechanism of high-temperature nickel-based alloy with single abrasive grain. Grinding mechanism of high-temperature nickel-based alloy
احصل على السعر
Mineral Crushing and Grinding Circuits Semantic Scholar
Mathematical modelling and automatic control of mineral crushing and grinding circuits have been studied at the Queensland Julius Kruttschnitt Mineral Research Centre for several years. While much is still to be done, it is considered that knowledge of the subject has reached the point at which a useful monograph may be published. The emphasis in The main characteristic of crushing is that the tool and the grinding wheel should have exactly the same circumferential speed, i.e. a speed ratio q d = 1. This will avoid a relative velocity between the two bodies, resulting in lower wear of the profiling tool [6].Contrary to profile crushing the crushing speed v sd in form crushing is about 10 Form crush dressing of diamond grinding wheels ScienceDirect
احصل على السعر
PROCESS DESIGN AND IMPLEMENTATION TECHNIQUES FOR SECONDARY CRUSHING
By understanding the ore breakage characteristics and utilising comminution circuit modelling, the benefits of SAG mill feed size manipulation can be readily assessed. This paper looks at the benefits and problems of total secondary crushing of mill feed and advocates partial secondary crushing as a means of improving grinding efficiency for The field was eventually named “mechanochemistry” by Wilhelm Ostwald in 1891. A Cornish Crushing Machine Worked by a Steam Engine from “The Playbook of Metals” (1862) by John Henry Pepper Science History Institute. Crushing remained essential for preparing materials during the 1800s, but research into mechanochemistry waned.Mechanochemistry: The Science of Crush — Google Arts
احصل على السعر
Choosing the right strategy: cryogrinding vs. ball milling
The peaks at 1113 cm −1, 1025 cm −1 and 1068 cm −1 belong to various C–OH stretching of hydroxyl groups. 51,52 The absorption band at 1025 cm −1 (C5–OH stretching) intensified and became more pronounced with an increase of grinding time while a peak at 1068 cm −1 (C3–OH stretching) slightly shifted to a lower wavenumber Asst.Prof. Dr. Ayşe KALEMTAŞ COMMINUTION Comminution entails reducing the particle size of the raw material by crushing, grinding, and milling or fine grinding. In mineral processing parlance, comminution in coarse range is known as “crushing” and in fine range it is called “grinding”. Comminution : The act or process of reduction of particle size withCERAMIC MATERIALS I
احصل على السعر
A Critical Review on the Mineralogy and Processing for High
High-purity quartz (SiO2) is an important material widely used in many industries, including semiconductor technology, telecommunication, and optics. The content and distribution of impurities in quartz significantly affect the processing methods. This paper provides an insightful review on the processing of high-purity quartz, covering the Other techniques, such as heat treatment before comminution (milling in this case), were also used in processing to remove the cement paste (Shima et al., 2005, Tomosawa et al., 2005), but the energy consumption and generated CO 2 emissions could not be justified with the recycled aggregate improvement (Quattrone et al., Comminution and sizing processes of concrete block waste as
احصل على السعر
Mechanical Alloying: A Novel Technique to Synthesize Research
Abstract. Mechanical alloying is a solid-state powder processing technique that involves repeated cold welding, fracturing, and rewelding of powder particles in a high-energy ball mill. Originally developed about 50 years ago to produce oxide-dispersion-strengthened Ni- and Fe-based superalloys for aerospace and high A fundamental understanding of the grinding mechanisms is needed in order to provide a technological basis for cost-effective machining of ceramic materials. Most past research on ceramic grinding has followed either the "indentation fracture mechanics" approach or "machining" approach. The indentation fracture mechanics approach would Grinding Mechanisms for Ceramics ScienceDirect
احصل على السعر
Existing and New Processes for Beneficiation of Indian Iron ores
The iron ore industries of India are expected to bring new technologies to cater to the need of the tremendous increase in demand for quality ores for steel making. With the high-grade ores depleting very fast, the focus is on the beneficiation of low-grade resources. However, most of these ores do not respond well to the conventional Sample processing involves reducing the material size to ensure samples for homogeneity and extraction into a suitable matrix for analysis. The most common method for obtaining a homogeneous sample is grinding or comminution. Grinding samples allows for a reduced sample size in order to increase accuracy and decrease uncertainty.Principles of Sample Preparation by Grinding or Comminution
احصل على السعر
(PDF) Overview of Mineral Processing Methods ResearchGate
Size reduction typically involved crushing, grinding, and screening (Balasubramanian, 2015) and various separation techniques were employed dependant on the mineral of interest.DOI: 10.1016/J.CEMCONRES.2005.09.011 Corpus ID: 135569923; The influence of grinding mechanism on the liberation characteristics of clinker minerals @article{Celik2006TheIO, title={The influence of grinding mechanism on the liberation characteristics of clinker minerals}, author={Ilkay B. Celik and M. Oner}, journal={Cement The influence of grinding mechanism on the liberation
احصل على السعر
Crush Injuries of the Hand Part I: History, Mechanism and
This chapter, the first of two; deals with the basics of crush injuries of the hand as opposed to crush syndrome. The definition is explained and the differences are outlined. A journey through the historical review of the causative mechanisms gives the reader an insight into the machines inflicting a spectrum of injuries and their sequelae.
احصل على السعر